At Acoplastic, we constantly optimize the way we can protect the environment. Here you can read about the measures we have taken internally to increase sustainability and reduce the impact on the environment.
Processing and reuse of plastic shavings
For more than 16 years we at Acoplastic have been sending all our sintered virgin PTFE and TFM shavings to be processed and recycled. We also reuse about 95 percent of our none-sintered shavings.
As a spin-off of our participation in the CLEAN project by Force Institute, Acoplastic has initiated a cooperation with two other PTFE processing companies focusing on also utilizing shavings from sintered compounds (PTFE with fillers). Until now this has been perceived as impossible and not cost beneficial.
Furthermore, we also participated in the Wastelife project by Teknologisk Institute in 2022. This was regarding recycling of residual flows from our plastic processing. Despite challenges with handling and finding buyers, we have increased the proportion of recycling by 12.4 percentage points in 2022 compared to 2021 – from 17.8 percent in 2021 to 30.2 percent in 2022. We are proud of the initiative, and we continue to enthusiastically support and follow the development of methods to utilize sintered shavings.
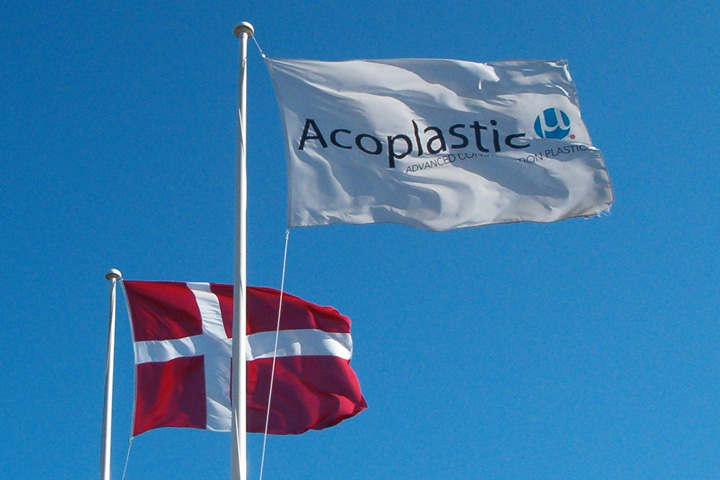
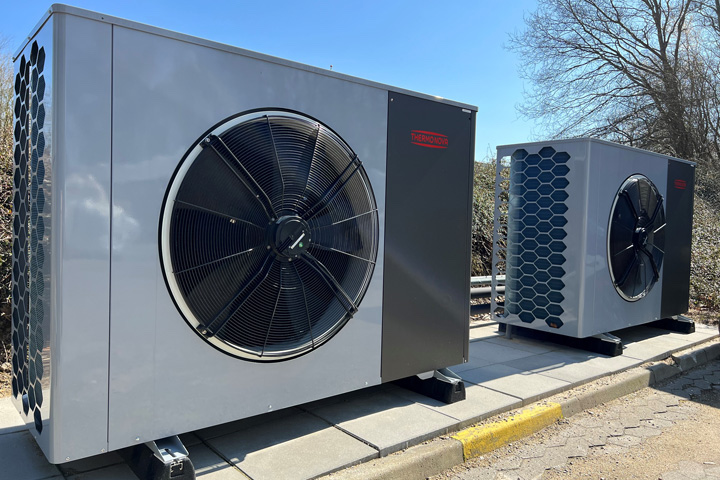
Air-water heat pump system
In 2022, we invested in an air-water heat pump system for the heating of the building and service water. The facility was installed in September and in 2022 alone it resulted in a saving of 31.6 percent in energy consumption for heating.
In 2023, an investment has been made in a Genvex-unit for the utilization of excess heat from our ovens, which is used for sintering PTFE. Subject to changes in our use of the ovens, the supplier’s estimate of energy savings is up to 60 percent.
Also, in 2023, an optimized control protocol of our vacuum suction system will be installed, which according to the supplier’s calculations will give an energy saving of approximately 30 percent in that area.
Air-water heat pump system
In 2022, we invested in an air-water heat pump system for the heating of the building and service water. The facility was installed in September and in 2022 alone it resulted in a saving of 31.6 percent in energy consumption for heating.
In 2023, an investment has been made in a Genvex-unit for the utilization of excess heat from our ovens, which is used for sintering PTFE. Subject to changes in our use of the ovens, the supplier’s estimate of energy savings is up to 60 percent.
Also, in 2023, an optimized control protocol of our vacuum suction system will be installed, which according to the supplier’s calculations will give an energy saving of approximately 30 percent in that area.
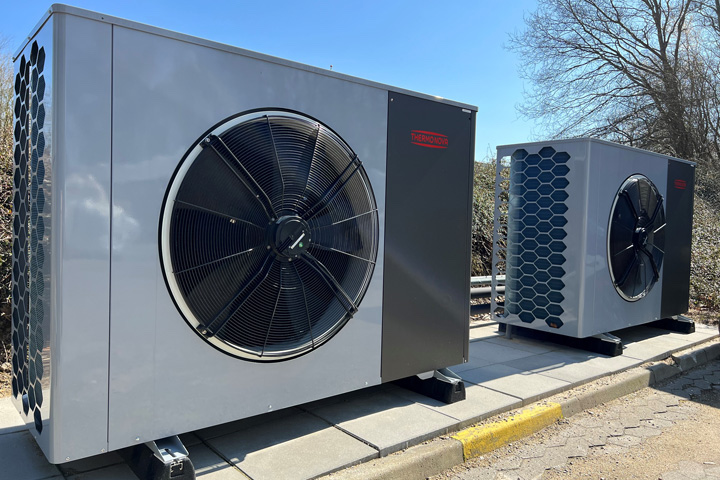
Optimization of transport and investment in education
We have an ongoing dialogue with our suppliers about packaging, transport, product optimization etc., with a focus on reducing our environmental impact. 91 percent of our raw material purchases in 2022 were made from suppliers who are ISO14001 certified. In addition, all internal transport takes place exclusively with electrically powered trucks. We also started a project that focuses on renewing company cars into electric-powered cars. So far, half of the cars have been replaced.
In 2023, we have signed up for Klimaklar SME/DI, which will strengthen our skills in relation to calculating our environmental impact and thereby improve our performance in relevant focus areas. Acoplastic has participated in Helsingør Municipality’s Green Business Salon meetings, where various speakers have talked about green transition. We have a regular contact with Erhvervshus Hovedstaden, which helps us with information about knowledge centres, projects etc. in relation to the green transition. Green transition is an important priority for us, and therefore we see this as an area in which we should invest a large part of our capacity.
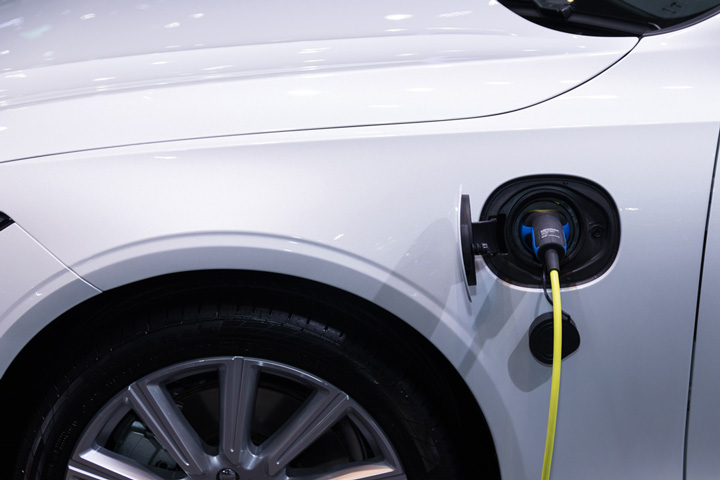